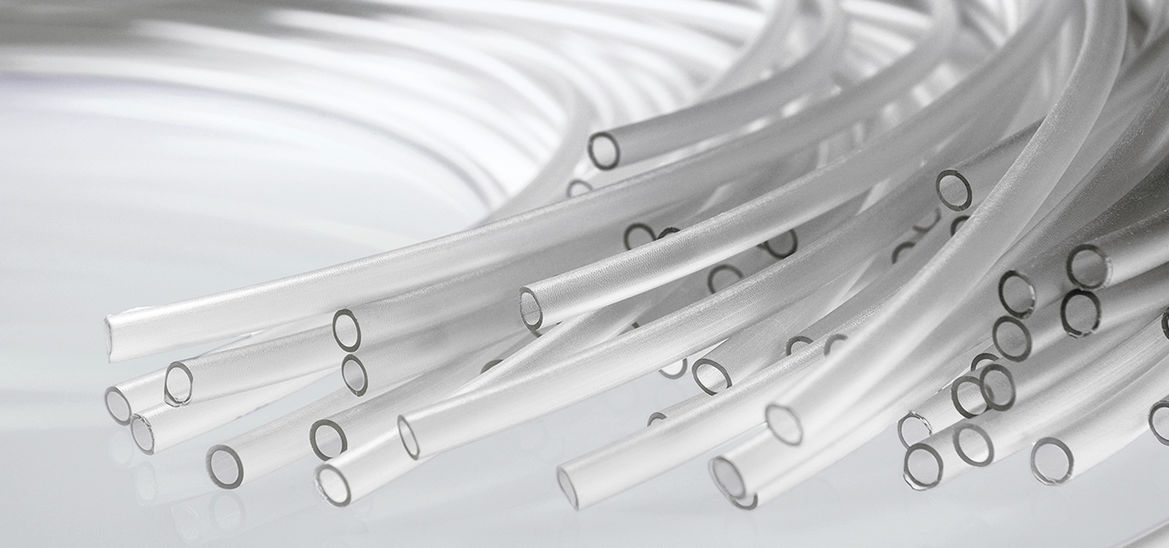
Versatile high consistency rubbers for medical devices
Our NuSil® brand of high consistency silicone rubbers (HCRs) from Avantor® deliver proven biocompatibility and versatile physical properties.
OPTIMIZE MANUFACTURING WITH BIOCOMPATIBLE HCRS
Medical device production demands silicone components formulated to deliver biocompatibility in the patient and versatility in manufacturing. Whether you’re extruding tubing, calendering sheeting or molding long-term (> 29 days) implantable devices, our HCRs can be tuned to end-use requirements and fabrication processes, such as extrusion, transfer or compression molding and calendaring.
NuSil HCRs set the standard for purity and reliability in the medical device industry
- Range of curing system options, including peroxide-catalyzed and platinum-catalyzed HCRs, as well as uncatalyzed HCRs
- Formulated for proven biocompatibility with strong regulatory and documentation support for applications such as balloons, O-rings, stoppers and septa, and diaphragms
- Shapeable “green strength” consistency that will hold its shape until cured
Choosing the right HCR for your application
With versatile physical properties and proven biocompatibility, NuSil HCRs are well-suited for a full range of medical applications and fabrication methods. Our formulas can be customized to your process and end-application performance requirements.
This infographic explores how to choose the right highly purified silicone for your application based on several key considerations:
Find HCR products
Use our product search to find the right HCR solution for your application.
Download content |
||||
Browse additional resources related to fluorosilicones. | ||||
![]() |
![]() |
|||
Versatile silicones for medical devices | Thinking outside the conventional silicone box | |||
![]() |
||||
High consistency silicone rubbers: Important material properties for healthcare applications |
Frequently Asked Questions
High consistency silicone rubbers (HCRs) consist of high molecular weight siloxane polymers combined with silica to produce a silicone that has a clay-like consistency in its uncured form. HCRs offer versatile physical properties and proven biocompatibility, making them well-suited for a full range of medical and implantable applications and fabrication methods. Whether you’re extruding tubing, calendaring sheeting or molding components for medical devices, NuSil HCRs can be tuned to specific processing and end-use requirements.
One of the most unique properties of HCRs is its “green strength.” Uncured HCRs have a clay-like consistency that can be shaped into a given dimension or form and will hold that shape until it is cured. NuSil offers both peroxide-catalyzed and platinum-catalyzed HCR systems, as well as uncatalyzed HCRs.
HCRs exhibit a range of physical properties that make them ideal for demanding applications, including:
- Excellent mechanical properties (tear strength, elongation, and tensile strength)
- High thermal stability, withstanding extreme temperatures
- Superior electrical insulation properties
- Resistance to chemicals, UV exposure, and environmental stress
- Biocompatibility for biomedical applications, including long term implants
- Strong resistance to deformation under mechanical stress
Due to these properties, HCR is widely used in the design of medical devices, including long term implants and drug delivery combination devices.
Long-term implantable and drug delivery / excipient materials are available for certain applications. These materials are supported with FDA Master Access Files (MAF) and Drug Master Files (DMF).
Finished products using HCRs typically use one of the following three main types of fabrication processes:
- Extrusion: For continuous profiles, such as tubing, ribbon or rod. In this process, the HCR is forced through a die to craft the intended shape. It is an efficient processing method that offers design flexibility.
- Compression or transfer molding: Best suited for creating solid or hollow parts, such as cuffs, valves or balloons. Typically, transfer or compression molding with HCR is a more economical molding process for low to medium volume parts.
- Calendering: Creates continuous sheeting for further processing such as die-cutting or slitting, to incorporate reinforcing layers or apply a silicone coating to a film or fabric. The HCRs are processed through a series of rollers that form and flatten the material into sheets with thicknesses ranging between 0.005 to 0.250 inches.
HCR is widely used in medical devices and implantable devices due to its superior biocompatibility, chemical resistance, and long-term stability. Some key benefits include:
- Compliance with FDA, ISO 10993, and USP Class VI standards for medical-grade materials
- Long-term implantable and drug delivery materials available for certain applications Supported with FDA Master Access Files (MAF) and Drug Master Files (DMF)
- Resistance to body fluids and many sterilization processes
- Excellent durability over the lifespan of the device
- Non-toxic and hypoallergenic properties, making it safe for direct skin contact
Most HCRs are supplied using either peroxide-catalyzed or platinum-catalyzed cure systems. In peroxide-catalyzed systems, curing is not initiated until the HCR is exposed to heat. This translates into a very long work time (table life), which is beneficial for molding or extrusion. When using peroxide-catalyzed HCR systems, a post-curing process is often required to remove residual byproducts.
By contrast, platinum-catalyzed systems commonly consist of two components: one contains the platinum catalyst, and the other contains hydride functional cross-linkers. When combined, the HCR retains its pre-cure consistency for a limited time and can be processed without undesirable byproducts produced during curing, often removing the need for a post-cure.
NuSil brand HCRs can be customized for specific medical device applications. We understand that every medical device has specific performance requirements which often require modifications or custom silicone formulations to achieve optimal performance while maintaining the desired level of biocompatibility.
Customer support
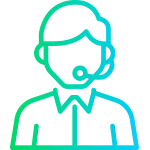
Contact us
Ready to move your next innovation forward? NuSil can help.
The Industry Leader in Biocompatible Silicones for Medical Devices
NuSil silicones have been trusted for over 40 years for use in the most demanding applications. Our best-in-class product lines are the premier choice in the medical device industry. Today, we have over 3,000 standard products that can be mass customized to help optimize your manufacturing processes and perform to your end-use requirements.
© 2023 Avantor, Inc. | Terms of use | Privacy policy